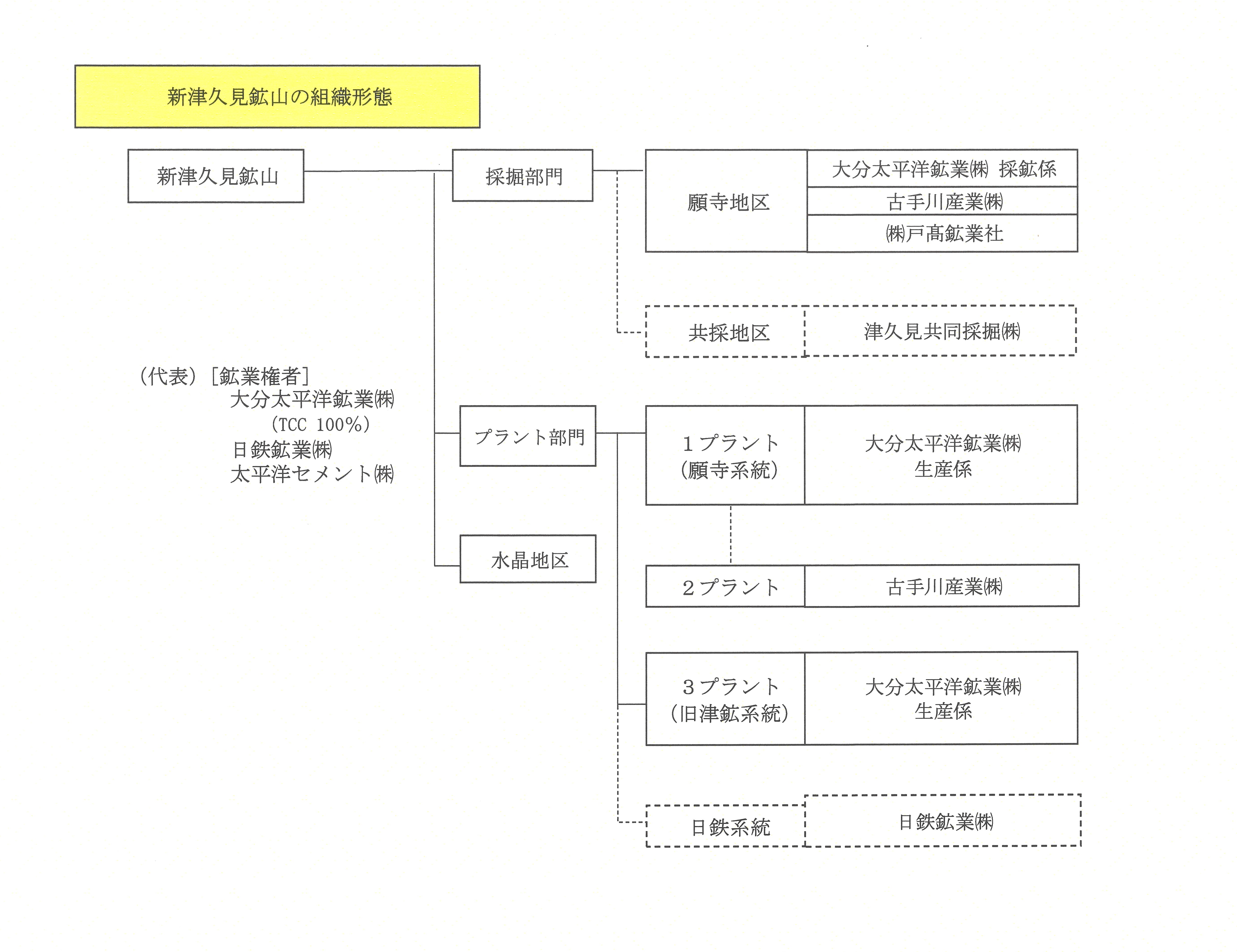
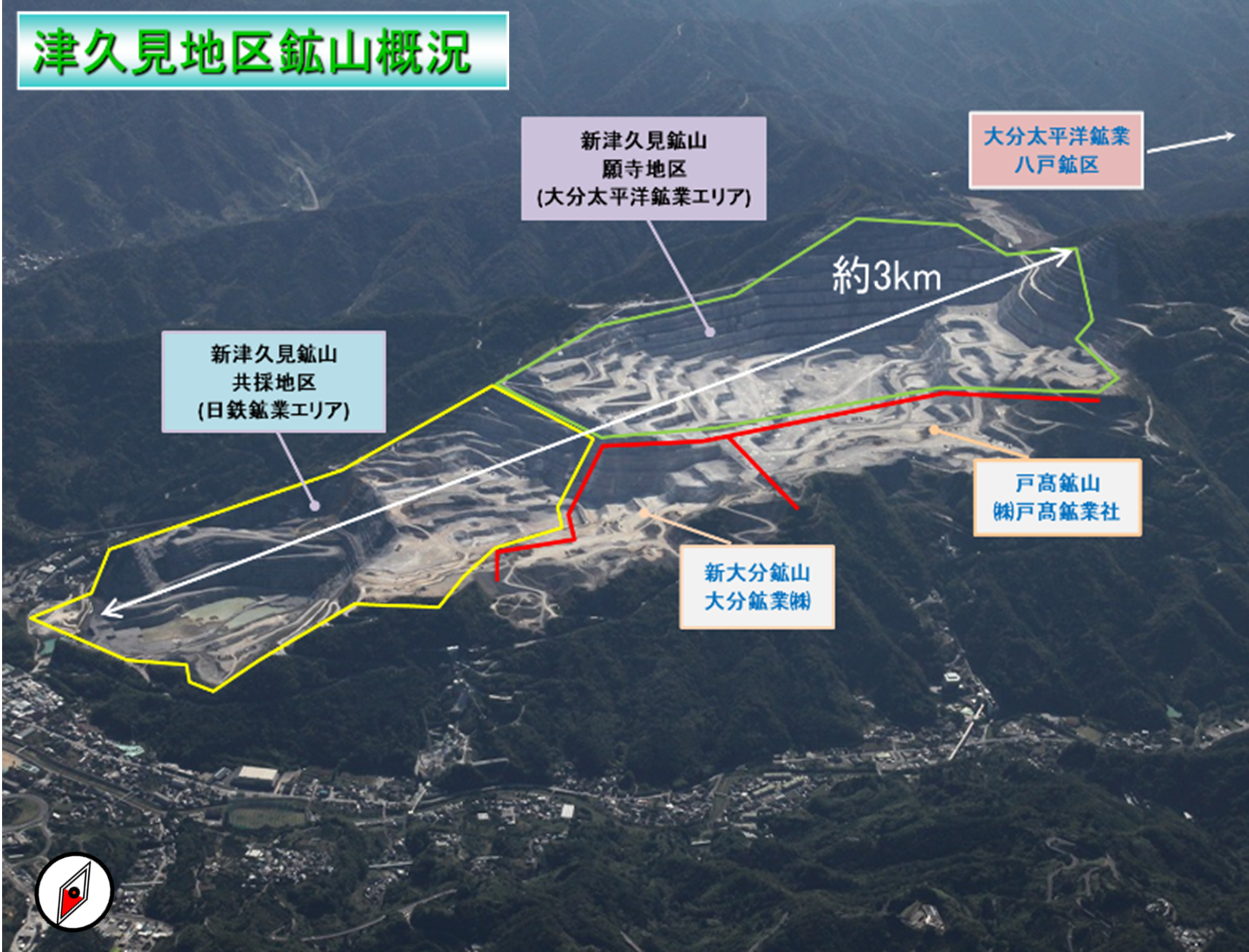
鉱山での採掘から出荷までの流れは以下の図の通りとなります。
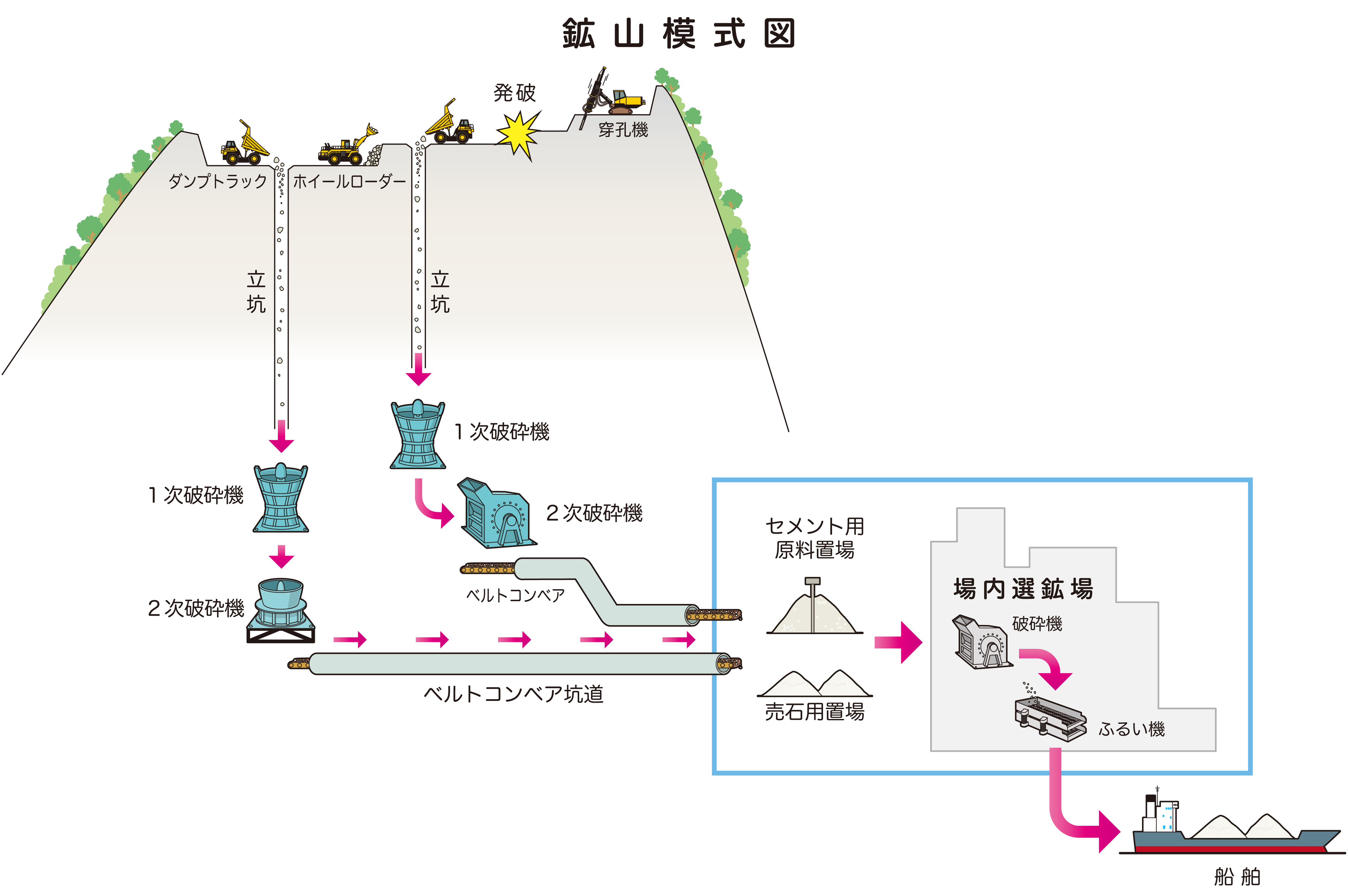
鉱山での採掘
①穿孔機による穿孔
1段の高さ5メートルから15メートルの採掘現場に合わせて、穿孔機を使い直径6センチから13センチの穴を一つの発破箇所で10~20本程度開けます。
②発破
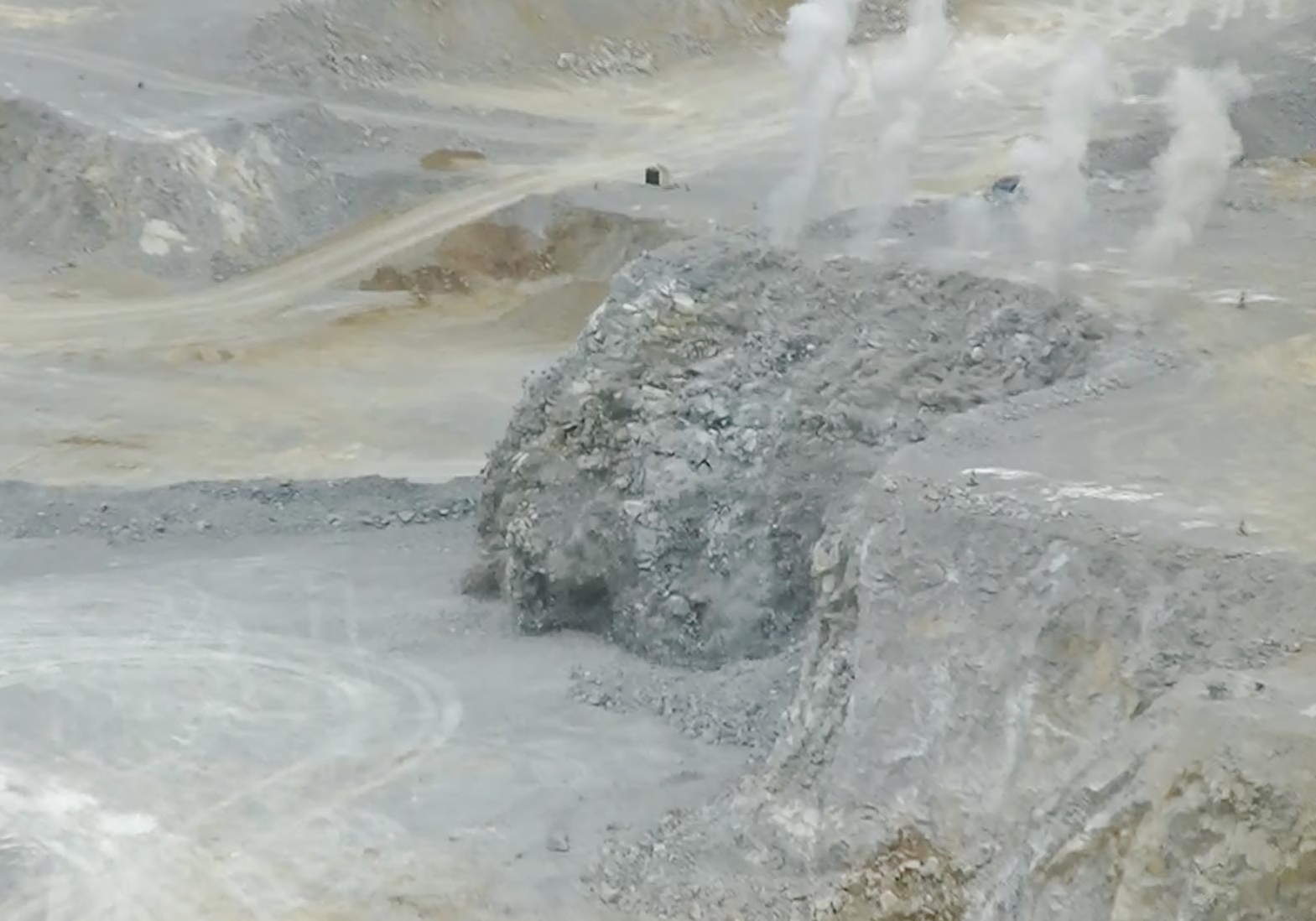
開けた穴に爆薬を詰めて発破を行います。発破には、比較的安全で安価な「アンホ爆薬」というものを使用しています。
願寺地区と共採地区では近隣住宅地への距離が違うため、発破箇所ごとに爆薬の量や穴の間隔を調整して騒音・振動・発塵を最小限に抑える工夫をしています。
③ホイールローダーでのダンプ積込
発破で砕かれた石灰石は、1回で20トンすくい上げる大型ホイールローダーで、90~100トン積みの大型ダンプに積み込まれます。
④立坑への投入
大型ダンプに積み込まれた石灰石は、立坑に投入され、地下の破砕機に送られます。
新津久見鉱山では、願寺地区と共採地区それぞれに2~3本の立坑があり、石灰石の品質により立坑を使い分けて、様々な用途に向けた石灰石を出鉱しています。
新津久見鉱山では、国内最大級の重機が使用されており、油圧ショベル8台、ホイールローダー13台、ダンプトラック14台、穿孔機8台、ブルドーザー1台、
割岩機1台が稼働しています。
破砕・選鉱
①坑内での破砕・ふるい分け
立坑に投入された石灰石は、破砕機で10センチ以下に砕かれます。この破砕設備は地下空間にあるため、騒音や粉じんが外部に出ないようになっています。
②ベルトコンベアによる輸送
破砕機で砕かれた石灰石は、願寺地区、共採地区それぞれ専用のベルトコンベアに乗せられ、鉱山から貯鉱場まで運ばれます。
ベルトコンベアは全長3キロあり、1日に約5万トンの石灰石が運ばれます。このベルトコンベアは「騒音防止」「粉じん防止」のため完全に密閉されています。
③プラントでの貯鉱・選別
(第3プラント貯鉱場)
(第1プラント貯鉱場)
貯鉱場に貯蔵された石灰石は、3か所の製品プラントで用途に応じ破砕とふるい分けを繰り返し、石灰石製品として出荷されるのを待ちます。
破砕機やふるいは建物内に設置され、騒音や粉じんを防止しています。また、粉じん防止のため、製品に散水を行っています。
出荷
各種製品は4つの桟橋から、日本全国および海外に出荷しています。
ここでも、貯鉱場と同様に散水を行い粉じん防止に努めています。